Hydroelectric power | Hydroforming technology at Touratech
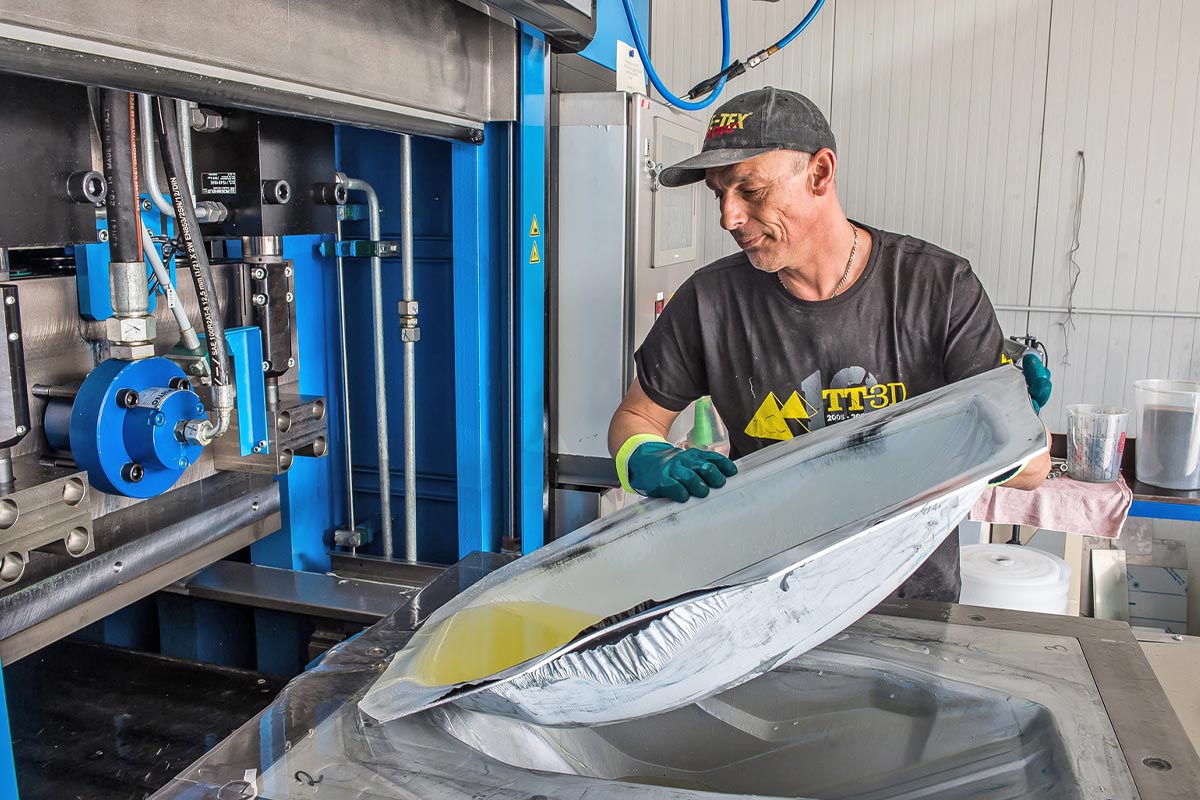
Touratech has been using hydroforming for eight years. The technology offers developers and designers interesting possibilities for product design. The process shows its advantages especially with the complex shapes of the engine protectors from the Rallye series.
It sounds quite simple: using the power of water to bring sheet metal parts into a desired shape. No wonder that this effect has long been used in so-called tube hydroforming. Exhaust bulbs for two-stroke engines, for example, are manufactured cost-effectively and in large quantities using this process.
However, the new sheet hydroforming process is not quite as simple. Therefore, the Touratech developers had to do pioneering work in many fields to be able to use the process for the production of numerous stainless steel and aluminium products. This starts with work preparation, because even the cutting and preparation of the sheet metal inserted into the machine, the so-called blank, is anything but trivial. Only when the blank is perfectly dimensioned, material can flow out of the flange area during the forming process at exactly the required rate.
And there are the enormous pressures that have to be controlled in the fixture. Around 2000 bar and more are required to form a four-millimetre-thick stainless steel blank.
The toolmaking is not to be neglected in hydroforming, which requires extensive know-how. Highest precision is required to mill the mould into which the component is pressed from high-strength tool steel. However, in contrast to classic deep drawing, only one half of the tool is needed, which is already one of the main advantages of the process.
But hydroforming offers much more. For example, almost any small radius can be realised with the technology, and the repeatability of the process is also very high. Particularly in the area of flat protectors, such as cylinder or engine protectors, hydroforming enables complex shapes that guarantee a significant increase in protection.