In search of perfection
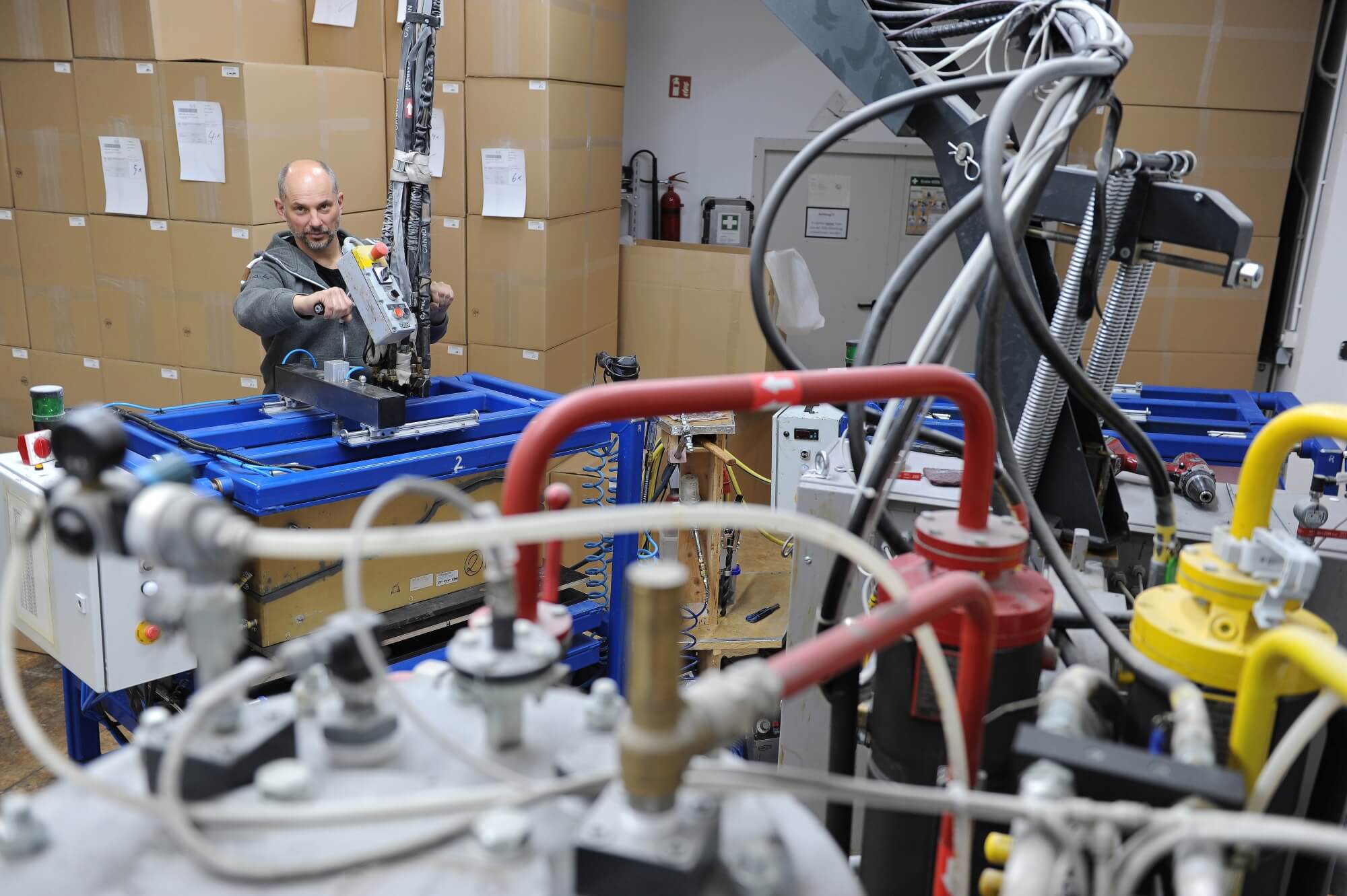
How Touratech seats are made
As the central interface between rider and motorcycle, the seat plays an important role in on-bike comfort. Touratech seats are manufactured at Crew68 in Murnau, using fine craftsmanship and modern technology.
As the upper part of the mould is slowly lifted with a slight hiss of the pneumatic system, the inexperienced bystander can sense a tension in the air, like waiting to see if you‘ve won the lottery. Dirk Bendl, on the other hand, is completely relaxed as he watches the action. He reaches into the mould, takes out a deep black seat shell for a Yamaha Ténéré 700, lets his gaze glide critically over the workpiece and nods with satisfaction.
He is the 52-year-old boss and owner of Crew68, a company specialising in prototype construction, design development and small series production in Murnau, Upper Bavaria - where the seats for Touratech are manufactured according to strict quality specifications.
The development of a seat shell is not just about maximum precision, although this is of course indispensable for the subsequent fit. It is crucial that the developers also take into consideration all the possible variants of the seat right from the outset. This is because Touratech seats are available for numerous motorcycle models, not only for those with the standard seat height but also for the higher and lower variants, designed to suit different rider sizes. The „Rallye“ type seats are a speciality. They replace the two-piece seats, favoured by numerous motorcycle manufacturers, with a one-piece seat whose design is as sporty as it is ergonomic, giving the rider optimum freedom of movement, especially when riding off-road.
Back to the development process. In addition to countless empirical values, personal impressions gained through riding the respective motorcycle also flow into the concept for each individual seat. This means, for example, that the Touratech seat is wider in certain places than the original, that irritating edges are avoided, or that a different contour is chosen.
Once the specifications are complete, the motorcycle’s measurements are taken. And now the model building begins. A „master sample“ is created by hand, using plastic elements, adhesive and filler. Depending on the planned number of pieces, the mould for series production can be taken directly from this „master sample“ or it can be digitised three-dimensionally. The data for the toolmaker is then generated in a CAD program.
As soon as the mould has been created, series production can begin. For this, Crew68 relies on the proven Resin Injection Moulding process, RIM for short. In this process, two synthetic resin components are mixed together and injected into a mould where they cure rapidly. For the Touratech seat shells, the creative minds at Crew68 have chosen a mixture ratio that gives the plastic a high degree of stiffness - but at the same time, its consistency remains soft enough to allow the cover to be stapled in place.
Production of the seat shells using the RIM process.
Before the seat shell is passed on to the next production step, fastening elements are attached.
The seat foam - more than just bubbles
The quality of the foam core is essential for the comfort of a motorcycle seat. Dirk Bendl and his crew have put countless hours into the development of foams. The exact mixture ratio of the two components, the pore size as well as the volume used - all these parameters are varied umpteen times until they have found the perfect composition for a foam. And there is not even THE one foam for Touratech seats. An individual formulation is developed for each model.
The foaming of a seat core.
"The high seats tend to need a firmer foam,“ Bendl explains. This is necessary to prevent the core from deforming laterally, for example when centrifugal forces act on the rider. For lower seats, you also need a slightly harder mixture. This apparent paradox arises from the fact that the upholstery, given its thinness, would otherwise loose its shape very quickly.
In addition to the mechanical properties of the foam core, its shape naturally has a major influence on ergonomics, i.e. on the posture of the rider when sitting on the motorcycle. The developers pay special attention to an optimal knee angle. This can be varied according to the size and leg length of the rider by adjusting the height of the seat, i.e. the thickness of the foam core. The angle of the seat surface in relation to the horizontal also plays an important role. If, for example, the seat is tilted too far forward, the rider slides further and further forwards as the journey proceeds, even without strong braking. „If the sitting angle is ideal, the pelvis is tilted into an upright position, which relieves pressure on the lumbar spine,“ Bendl explains. The foam‘s resistance to sagging also contributes to correct pelvic positioning – and, as a result, to a healthy rider posture. If the foam keeps its shape, pelvis and spine also remain in their correct position. If, however, the foam gives way too much, the rider also slumps. The developers attach great importance to the ergonomic design of the seat, because this is where contact between human and machine takes place. The groove in the seat surface is typical for Touratech seats. This relieves the coccyx and, in conjunction with an upright pelvic posture, ensures that the main load rests on the two ischial bones.
The foam formulations are varied depending on the model.
The perfect shape of the seat core is determined in an elaborate process for each motorcycle model. To do this, foam blanks are processed with a belt sander until the contour and surface allow an ideal sitting position. The mould for the serial foaming process is then taken from this sample.
The cover - high-tech and handmade
The last important component of a Touratech comfort seat is the cover. „We have been manufacturing shells and foam cores for Touratech seats for many years. Because we now carry out the upholstery work involved in fitting the cover in-house as well, we make and supply the complete product,“ explains Dirk Bendl. This step became necessary because Kahedo, Touratech‘s long-time partner in seat production, closed its doors at the end of last year. As with many medium-sized companies, no suitable successor was found for founder and company boss Karl-Heinz Dorn. But fortunately, the expertise of the traditional Swabian company has not been lost. „We have been able to take over a lot of know-how from Kahedo with regard to seat covers,“ Bendl is pleased to say. The extensive knowledge transfer ranged from basic knowledge about the ideal placement of seams and the different materials, to tricks of the upholstery trade.
Touratech uses „Fresh Touch“ seat covers as standard. The surface coating of this material reduces the temperature of the seat cover by up to 10 degrees Celsius, by reflecting the infrared component in sunlight.
The „DriRide“ cover offers even more comfort at high temperatures. In this product, a membrane ensures that moisture is conveyed away from the body through the cover and expelled through the side of the seat. Like the „Fresh Touch“ versions, these covers are, of course, also one hundred percent waterproof.
Fitting the cover is the final step in the production of the seat. Experience and dexterity are necessary to pull the fabrics tightly over the core - wrinkle-free. Finally, the material is stapled to the shell.
Around 600 seats a month are produced at Crew68. Due to the high proportion of manual work, seven specially qualified employees are exclusively responsible for the Touratech seats, from the development stage, through the production of the shell and foam core, to the upholstery.
Taking careful motorcycle measurements is one of the prerequisites for the optimal fit and mountability of the seat.
"Thanks to Touratech‘s decades of experience in seat development, as well as the wide range of variants and our handcrafted production, customers receive products of the highest quality that are precisely tailored to their needs,“ says Dirk Bendl, not without pride, as he critically examines a seat that has just been completed.
The complete range of Touratech seats is available at
shop.touratech.com/vehicle-equipment.html?cat=721
From left: Original seat of a Yamaha T7, master sample of the seat pan, Touratech seat pan, sample for the foam mold, foamed core, finished Touratech seat.
How Touratech seats are made:
- The adhesive is sprayed onto the cover and foam core.
- The cover is prepared for mounting.
- Fixed points are marked on the foam core for correct positioning.
- The hot air gun makes the cover supple.
- A lot of experience is necessary for exact, wrinkle-free covering of the seat.
- Once the position is correct, the cover is stapled to the shell.
- Final, fine corrections with the help of the hot air gun.
- Tested and approved: after assembly, the final inspection.
- Covering the Touratech seats is classic upholstery work.